“How often should we inspect?”
Many companies answer that question by referring to the applicable regulations. They’ll say, “We have to inspect once a week,” or whatever the requirement is, and that’s how often they’ll inspect.
But the regulations are only the minimum. Legally required inspection schedules aren’t necessarily the most-productive inspection schedules for your company—in fact, they probably aren’t. Inspections increase safety, and that decreases cost, so it’s usually in a company’s best interest to inspect more often than required.
There’s also the matter of liability protection. Even if not mandated by regulation or law, documented inspections demonstrate “due diligence” by the company with regards to its safety processes. Documentation of regular inspections, above and beyond what a company has to do, can play a key role in defense against liability claims.
When thinking about how often you should inspect, you should of course be sure to comply with regulations. But the primary focus should be on how often you need to inspect to ensure you’re maximizing the cost-containment benefits of inspections, as well as protecting the company from lawsuits.
Equipment Inspections
Virtually any piece of equipment you can think of needs to be regularly inspected using equipment-specific inspection checklists to ensure the inspections are correctly done and to provide documentation. Regular equipment inspections ensure that:
- Equipment doesn’t put personnel in danger of tragic and costly on-the-job injuries.
- Any defects are repaired as soon as they arise, before they become more expensive to fix.
- Operations aren’t disrupted by on-the-job failures of mission-critical equipment.
- Personnel are paying attention to the condition of the equipment they use, which usually leads to better care of equipment.
- No one can reasonably claim the company was negligent about inspecting.
All of these reasons are justification for inspecting every piece of equipment before every use, which is the ideal.
In reality, it’s not always practical to require pre-use inspections for some types of minor equipment. But if the equipment has the potential to harm its users or others (e.g., on-road and off-road vehicles, forklifts, cranes, boom lifts), pre-use inspections are essential to protecting people and the company!
Using The Checker inspection checklists, it doesn’t take long at all to do a proper inspection that will safeguard the company against the disastrous financial results of on-the-job accidents, provide liability protection, and keep the equipment in good working order at the lowest-possible cost.
Workplace Inspections
In addition to regular inspections of specific pieces of equipment, companies also need to perform routine facility-wide inspections, conducted independently by senior management, operations management, and safety staff.
The ideal frequency of these facility safety inspections will depend on much more than what regulations require. Critical factors to consider include:
- The riskiness of your type of business.
- The number of shifts using the workplace.
- Total number of labor hours worked at the workplace.
- Familiarity of personnel with processes (e.g., a new workplace or new critical equipment may require more frequent inspections).
- Historical record of incidents/near-misses.
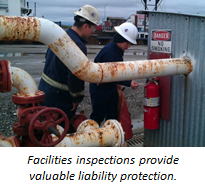
As with equipment inspections, The Checker inspection checklists for facilities can ensure that all necessary items are checked and that inspections are documented for regulatory compliance and liability protection.
This documentation can also be useful for internal management purposes such as maintenance and capital-investment planning.
Conclusion
How often you should inspect will depend on the equipment your company uses and the type of workplace you have—not on what the law requires. But in general, the more inspections, the better. Inspections shouldn’t be viewed as a chore—they’re a valuable tool to lower costs and mitigate risk.
Upper image courtesy of USAG-Humphreys, Creative Commons; lower image courtesy of U.S. Coast Guard, Creative Commons.